沥青路面施工工艺流程有哪些?
沥青路面施工的工艺流程主要包括以下步骤:1、施工准备:该阶段包括原材料的质量检测、配合比的确定以及施工场地的规划和清理。同时,工厂设备也必须进行校准和准备。
2、测量控制:测量人员必须根据施工规范和设备性能参数进行准确的放样工作,通常使用钢钉和红布进行标记。
3、材料运输:混合后的沥青混合料必须在集中搅拌站进行,并通过专门管理、有资质的运输车辆运至施工现场进行沥青摊铺。
4、摊铺沥青和成型:施工队伍需要将沥青混合料均匀、连续地摊铺在路面上,并保证压路机碾压过程中路面平整无痕迹。
同时,在过程中进行质量控制和必要的修整。
5、接缝处理:由于可能存在施工中断,会产生额外的横缝。
这一步主要是对这些接缝进行清理和处理,以保证路面的完整性。
6、健康安全:施工结束后,需要张贴标志并进行灌溉维护等措施,以保证路面质量,延长其使用寿命。
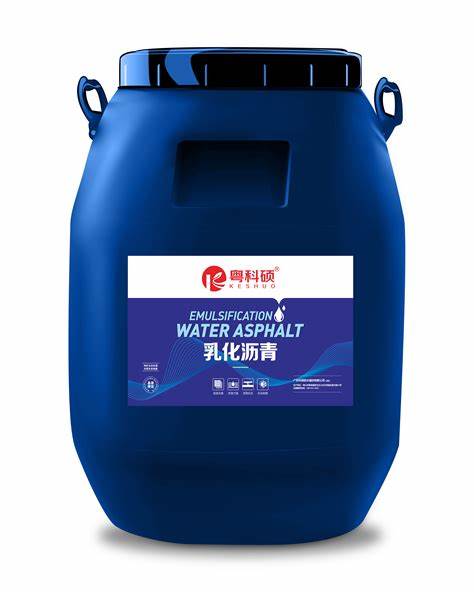
沥青混凝土摊铺机施工工艺流程如何?
构建过程如下。
1.施工准备过程包括原材料质量检验、材料准备、施工配合比确认、现场清理、设备状况确认等。
2.测量控制。
此过程涉及根据规范要求和设备参数设置测量员,通常用钢钉和红布进行标记。
3.过境。
该流程包括混合物的集中混合、合格车辆的统一管理以及包装准备材料的运输。
4.路面成型是设备进入设定点,以恒定速度连续压实,并用压路机碾压直至表面不留痕迹的过程。
、过程检验和修整。
5.联合加工。
这主要是指因施工中断而扩大的横缝的清理工作。
6.医疗保健包括标志设置、医疗保健洒水等。
沥青路面施工步骤
铺开矿物材料面积后,用两轮压路机碾压,力度为60-80kN。
滚压道路时,从路缘一侧滚到道路中间。
速度最初不应超过2公里/小时,然后可相应提高。
铺设第二层沥青,铺第二层矿物材料并碾压。
撒上第三层沥青,铺上第三层矿物材料,然后滚下来。
沥青结合料是在沥青混凝土混合料中起粘结作用的沥青材料(包括添加的外加剂、改性剂等)的总称。
它将矿物颗粒粘合成一个整体,增加涂层的强度和运动过程中对损坏的抵抗力,并且还使涂层防水。
沥青的作用:
沥青混凝土是由一定粘度和适当掺量的沥青混凝土材料和一定标号的矿物填料配制而成的。
混合物完全形成。
沥青混凝土作为沥青路面材料,在运行过程中必须承受车辆荷载的反复暴露和环境因素的长期暴露。
因此,沥青混凝土必须具有良好的抗自然因素的能力,同时具备一定的承载能力。
也就是说,必须具有高温环境下足够的稳定性、低温环境下的抗裂性、良好的耐水性、持久的抗老化性能和安全的防滑性能,才能保证沥青路面具有良好的使用性能。
求!水泥混凝土路面的施工工艺流程
一、施工准备1、准备质量检测的施工机械设备和工具1)主要机械(压路机、推土机、装载机、洒水车、混凝土搅拌车、搅拌机、振动梁、振动棒、压花机等)数量、型号、性能和施工保障能力应满足施工的最低配置要求,同时也满足工程进度要求。2)验证试验设备应能满足本工程施工质量和施工进度的基本要求。
2、控制原材料来源,按规定频率进行自检,并要求实验室按规定频率对原材料进行抽检。
不合格的材料不得进入现场,已进入现场的不合格材料必须清除出现场。
进场原材料必须有明显标识,主要包括原材料名称、产地、进场日期、数量、是否通过检验等。
3、堆料场和搅拌场1)搅拌场内粗、细骨料储存区应硬化防水防泥,分隔成料仓,并设有良好的排水系统。
水泥、生石灰、熟石灰分别仓库堆放,生石灰硝化装置符合环保要求。
水泥、石灰和细骨料需要采取防雨措施。
2)混凝土搅拌站应有明显的水泥混凝土、水泥稳定骨料、水泥砂浆、砂、石灰、碎石等混合料配合比标识,包括设计配合比和施工配合比。
4、混合料成分及配合比的设计承包商必须到实验室设计混合料的成分。
配合比设计包括:根据稳定物料指标的要求,通过实验选择合适的骨料、水泥和石灰,确定合格的骨料配合比、水灰比、水泥和石灰的掺量以及最佳配比。
水混合物的含量。
合理的配合比必须满足强度要求,热收缩和干燥收缩系数低(现场开裂少),施工和易性好(粗骨料离析小)。
5.仔细检查每个模型的高度。
如果高度不够,则必须移除模型。
2、检验检测:按规定频率检查原材料(砂石级配、含水率、含泥量、石灰、水泥)、水泥用量、石灰用量、配合比强度、挠度、压实度、厚度、宽度、平整度,横向坡度等3、施工工艺检查(一)、天然优质砂石路基A、试铺试验段1、底部承重层的检查天然优质砂石路基在摊铺前,需对路面的表面进行检查。
土路基(或砾石垫层)。
必须清除表面的浮土和积水。
2.通过试验铺装确定以下内容,为正式施工提供依据:1)确定一次性铺装的适宜厚度和松散路面系数。
2)确定标准施工方法。
例子:滚压机的组合:顺序、速度、道次数。
卫生维护的灌溉方法、时间和间隔。
3)确定各工作段的合适长度。
B、施工工艺检查1、施工现场检查1)碎石铺装前,应审查布局,核对挂缆的宽度、高度和线型。
2)施工段检查工作台面表面情况。
表面必须清洁且无浮土和水。
3)碎石路面应保证路缘厚度和坡度足够,路面平整度均匀。
4)检查摊铺后粗、细骨料的分布情况。
如果出现细骨料分离或粗骨料局部“巢”的情况,则需要专业人员的干预才能进行充分处理。
5)砂石碾压必须遵循生产试验部分确定的程序和工艺。
严禁车辆在已竣工(未加固)路段行驶。
6)旋压应达到规定的压实度,无明显轮痕。
2.原材料控制原材料是控制天然优质砂石底层地板施工质量的关键。
为确保路基符合质量要求,必须经常检查来料砂石和含泥量。
不允许对沙子和砾石进行分级。
3、保健1)每段轧制结束后应立即开始保健。
2)卫生方法:喷水养护、撒沙滚滚。
在滚动和检查之前,底层地板必须始终保持湿润。
3)底基层压实前必须封闭交通,禁止车辆通行。
C、检验施工完毕后,需对以下内容进行检验:挠度、厚度、压实度、平整度、中面偏差、纵坡度、宽度、横坡度。
(2)水泥稳定骨料或石灰稳定碎石基层A.试铺试验,第1节底部承载层检查1).碎石基层摊铺前,现场监理人员应对碎石基层表面进行检查。
必须清除表面的浮土和积水。
2)在制作水泥稳定骨料和灰砂砾石基层之前,工作面表面必须保持湿润。
2.通过试铺确定以下内容,为正式施工提供依据:1)验证施工所用骨料配合比和搅拌时间。
2)确定路面的适当厚度和松散路面系数。
3)确定标准施工方法。
示例:滚压机的组合:顺序、速度、道次数。
卫生维护的灌溉方法、时间和间隔。
4)确定各工作段的合适长度。
5)严格组织混合、运输、层压等工序,减少延误时间。
B、施工过程检查1、施工现场检查1)摊铺水泥稳定骨料或水稳定碎石前,需进行审查跟踪检查挂缆的宽度、高度和线型。
2)施工段检查工作台面表面情况。
表面必须清洁、无浮土、无水,并喷水润湿表面。
3)基层混合路面必须保证厚度恒定、松散路面系数恒定、路冠坡度合格、路面平整度恒定、接缝光滑。
4)检查摊铺后粗、细骨料的分布情况。
如果出现细骨料分离或粗骨料局部“巢”的情况,则需要专业人员的干预才能进行充分处理。
5)混凝土搅拌运输车进入施工现场后,必须有专人指挥停车、卸货。
6)混合物的碾压断面必须分层清晰,并设置清晰的界限标记。
遵循生产测试部分确定的程序和流程。
严禁在已竣工或正在进行的路段调头、急刹车。
7)碾压必须在试验确定的延迟时间内完成,并达到要求的压实度,不得有明显轮痕。
2.场内质量控制拌和场(场)是控制水泥稳定骨料和灰砂石施工质量的关键。
为保证混合料符合质量要求,主要应检查以下几项:1)混合前,搅拌站配制的材料应能满足地坪材料1-2天的要求。
2)开始每日拌合前,需检查现场各种骨料的含水率,并计算每日配比。
添加水与自然含水量之和应略高于最佳含水量。
水泥或石灰的实际用量可比设计混合物组成时确定的水泥或石灰用量高约0.5%。
3)每隔1-2小时检查一次混合情况,主要检查混合比和含水率是否发生变化。
4)装料时,车辆应前后移动,分3次装料,以免混合料离析。
3.医疗保健1)承保和医疗保健应在滚动的每个部分完成后立即开始。
2)卫生方法:将草袋或衣物打湿后,手工覆盖在卷好的基层表面。
2小时后,再次喷水。
基层必须在7天内始终保持湿润,并正常保持至少15天。
3)卫生期间,必须封闭交通,不允许车辆通行。
C、检验施工完毕后,需对以下内容进行检验:挠度、厚度、压实度、平整度、中面偏差、纵坡度、宽度、横坡度。
(3)水泥混凝土表层A.试验路面试验,第1节:下部承重层的检查1)浇筑水泥混凝土前,需对水泥稳定骨料或砂岩基层的表面进行检查石灰质砾石。
浮土和积水必须去除表面。
2)浇注水泥混凝土前,工作面表面必须保持湿润。
2.通过试铺确定以下内容,为正式施工提供依据:1)验证施工所用骨料配合比、水灰比和搅拌时间。
2)确定各工作段的合适长度。
3)复制好钢筋。
钢筋是根据复制图制作的。
钢筋的尺寸、数量、型号必须准确。
4)确定钢模脱模剂及用量,确定模板固定方式及曲率(弯曲)、垂直度等。
并确定脱模、抛光、压花、切缝的时间。
5)严格组织搅拌、运输、振动等工序,减少延误时间。
B、施工工艺检查1、施工现场检查1)在浇注水泥混凝土前,需要审核布置,检查模板间的宽度、模板的高度、路面的曲率和线型。
2)检查施工段工作面。
表面必须清洁、无浮土、无水,并喷水润湿表面。
3)混凝土搅拌运输车进入施工现场后,必须有专人指挥停车和卸货。
4)取出振动器时,速度要慢,以免产生空腔;振动时应握紧秤,以免漏水和振动过大,使混凝土充分密实,但时间不宜过长,以免引起离析。
振动梁运行过程中不应有孔洞、凸起,保证平稳。
在浇注过程中,需要密切注意模板变形和砂浆泄漏,一旦发生,应立即纠正。
混凝土压实后24小时内不得振捣。
5)吸水完成后,立即平整任何突出的石头或不平坦的区域。
最后用尺子检查路面的平整度。
如果符合要求,用铁抹刀手动抹平。
6)抹灰完成后,进行表面横向纹理处理。
压花时,必须控制好混凝土表面的干燥和湿度。
对于现场检查,可以手动测试混凝土。
确认合适后,在模板两侧放置槽钢,为压花机提供通道。
7)拆卸模具时要小心,避免损坏任何边缘或角落。
8)压槽完成后,安装护栏,防止人员踩踏或跑上路面,损坏路面。
9)横向收缩缝切割:横向施工缝采用锯缝,深度7cm,宽度5mm切割时必须保持充足的注水,过程中必须观察刀片的注水情况。
缝纫机启动时间(昼夜平均温度-5°,开始裁剪时间为4天;昼夜平均温度为0°,开始裁剪时间为3天;昼夜平均温度为15°时,起始切割时间为2天;昼夜平均气温20℃,1.5天即可开始砍伐;如果昼夜平均温度≥25℃,则需要1天才能开始切割)。
这里的初始切割时间是指混凝土抹平成型后所经过的时间。
10)将沥青水泥倒入锯缝中。
填缝前,必须清除接缝内的临时密封材料,并使接缝顶面与路面齐平。
2.场内质量控制混合料搅拌场(场)是控制水泥、混凝土施工质量的关键。
为保证混合料符合质量要求,主要应检查以下几项:1)开始混合前,对物料进行检查。
搅拌现场配制的材料应能满足1-2天的摊铺材料要求。
2)开始每日拌合前,需检查现场各种骨料的含水率,并计算每日配比。
添加水与自然含水率之和应略高于最佳含水率,并严格控制水灰比。
3)每隔1-2小时检查一次搅拌情况,检查配合比、水灰比是否发生变化。
4)装料时,车辆应前后移动,分3次装料,以免混合料离析。
3、保健1)混凝土浇筑完毕12小时后,即可拆模进行保健。
2)卫生方法:混凝土必须湿润,然后手工覆盖薄膜。
7天内加强补水保健,21天内定期保健。
3)卫生期间,必须封闭交通,不允许车辆通行。
C.检验施工完毕后,应进行以下检验:抽查混凝土抗弯强度、厚度、平整度、中面偏差、纵坡度、宽度、成型段的横坡度。